Digital Twins: The Virtual Side of Engineering
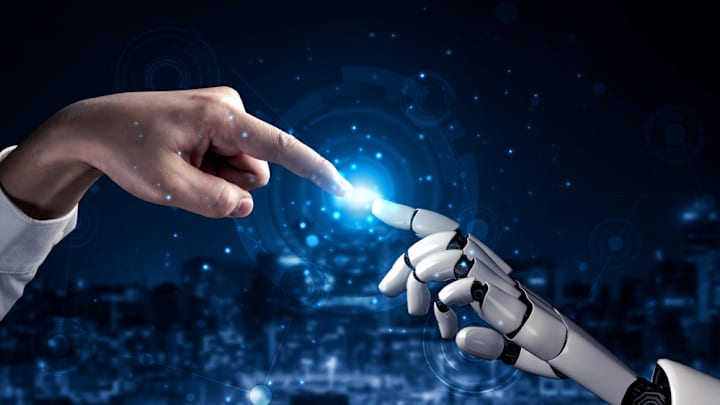
Imagine being able to test-drive a jet engine, fine-tune a wind turbine, or monitor an entire factory—without touching a single physical part. That’s not sci-fi anymore. It’s the power of digital twins: highly detailed virtual replicas of physical systems that allow engineers, designers, and decision-makers to explore, experiment, and optimize—without real-world risk.
Originally born in the realm of aerospace and heavy industry, digital twins have rapidly expanded into everything from smart cities to healthcare. They're more than just 3D models. They’re living, evolving simulations that are connected to real-world data in real time.
So, what makes a digital twin different from a traditional simulation? And how are they transforming the future of engineering?
Let’s take a closer look inside this powerful pairing of physical and digital.
What Exactly Is a Digital Twin?
At its core, a digital twin is a virtual model of a physical object, system, or process. But unlike a static diagram or CAD file, a digital twin is dynamic—fed by sensors and data from the real-world counterpart.
This continuous data flow allows the twin to mirror the physical object’s current state, behavior, and performance. Engineers can interact with it, simulate changes, predict future outcomes, and troubleshoot issues—all before making any physical changes.
Think of it as an always-on, always-updating digital shadow of something real.
How It Works: The Feedback Loop
Here’s how a typical digital twin system operates:
- Sensors on the physical object collect data—temperature, pressure, usage rates, vibrations, etc.
- That data is transmitted to a cloud platform or analytics engine.
- The digital twin, which includes a high-fidelity 3D model and simulation algorithms, updates in real time.
- Engineers or AI systems use this virtual twin to monitor, test, and optimize.
- Insights from the twin can be pushed back to the real-world object—adjusting performance or guiding maintenance.
It’s a constant feedback loop between the physical world and its digital reflection.
Key Benefits of Digital Twins in Engineering
- Real-Time MonitoringEngineers can view the health and performance of machines in real time—no need to physically inspect or guess. This is especially valuable for remote or hazardous locations, like oil rigs or offshore wind farms.
- Predictive MaintenanceInstead of waiting for a part to fail, digital twins help predict when it might fail based on data patterns. This reduces downtime, saves money, and keeps systems running smoothly.
- Design and TestingBefore building a prototype, engineers can simulate how a product will behave under different conditions. This shortens the design cycle and improves innovation.
- Training and VisualizationTeams can use digital twins for immersive training, helping workers understand equipment before they ever touch it. AR and VR integration makes this even more powerful.
- Sustainability and EfficiencyDigital twins can identify inefficiencies in energy use, materials, or logistics—leading to greener, more sustainable systems.
Where Digital Twins Are Already Making an Impact
- Aerospace: NASA pioneered early digital twin concepts to simulate and monitor spacecraft systems. Today, aircraft manufacturers use them to track the performance of engines, wings, and avionics.
- Automotive: Carmakers simulate crash tests, fuel efficiency, and even how software updates might affect driving performance.
- Manufacturing: Factories use digital twins to create "smart production lines" that can adapt in real time to changes in demand, supply, or performance.
- Urban Planning: Cities like Singapore are building digital twins of urban infrastructure to test traffic flow, public transportation systems, and emergency response plans.
- Healthcare: Digital twins of organs or even entire patients are emerging to model treatment outcomes before they’re applied in real life.
AI + Digital Twins = Next-Level Engineering
When artificial intelligence is layered onto a digital twin, it can begin to do more than reflect—it can optimize and anticipate.
- AI can analyze patterns in the twin’s data to make predictions
- It can recommend or even automatically implement changes
- It can run thousands of simulations in seconds to find the best design or fix
This kind of self-learning twin is particularly valuable in complex systems—like supply chains, energy grids, or large infrastructure projects.
Challenges and Considerations
Of course, digital twins aren’t magic. They come with challenges:
- Data Overload: Twins rely on high-quality, real-time data. Too much or inconsistent data can muddy the results.
- Security: Connecting real-world systems to the cloud raises cybersecurity concerns. A compromised twin could expose critical systems.
- Cost and Complexity: Developing and maintaining accurate digital twins can be resource-intensive, especially for legacy systems.
Still, as technology matures, these hurdles are shrinking—and the payoff continues to grow.
The Future: Twinning Everything?
As sensors become cheaper and cloud computing becomes more powerful, digital twins are likely to expand from individual machines to entire ecosystems. Imagine:
- A hospital with a digital twin that models patient flow, staffing, and equipment usage
- A farming operation with a twin that tracks soil health, irrigation, and crop yield
- A digital twin of a human body used to test new medications personalized to your biology
The future isn’t just one twin—it’s a network of connected twins, working together to simulate, optimize, and improve the world around us.
Virtual Vision, Real-World Impact
Digital twins are more than digital blueprints. They’re tools for prediction, prevention, and performance. They give engineers a safe space to ask “what if?”—and to find the best answers before anything breaks, wastes energy, or goes over budget.
And as this technology continues to evolve, the line between what’s real and what’s simulated will blur in the best way possible—giving us not just better machines, but smarter systems, safer cities, and more resilient solutions.
Because when you can test reality without the real-world consequences, innovation has room to thrive.